It was proven for the first time that controlled focusing was possible using only two electrical signals on a single-element transducer using the biaxial driving technique. We tested this on two different geometries.
Prismatic-shaped transducers
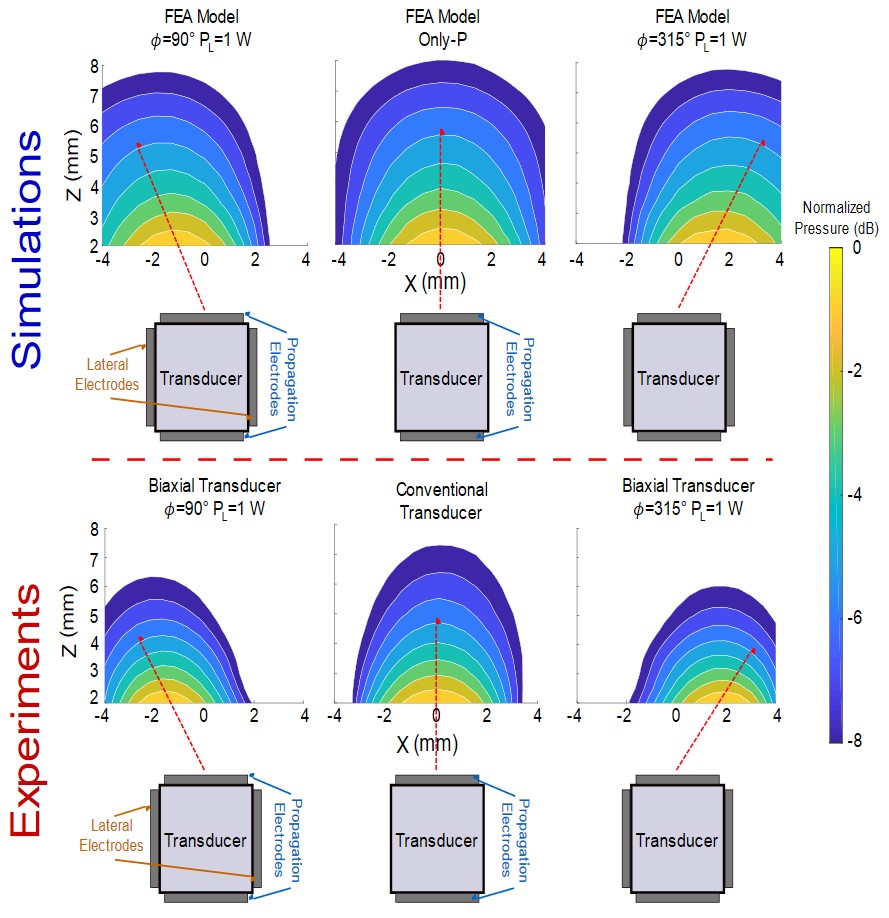
Prismatic-shaped biaxial driving transducers are built with two sets of electrodes: a pair along the propagation direction and a pair along the lateral direction. In prismatic-shaped ferroelectric materials poled along the thickness, an extensional deformation is produced along the length when an electric field is applied along this poling direction. An electric field applied orthogonal to this poling axis will produce a thickness-shear deformation. The biaxial driving combines both extensional and shear vibration modes on the transducer to control the acoustic beam direction. This is achieved by changing the phase angle and the power ratio between the orthogonal fields.
With a prismatic-shaped prototype transducer the ultrasound beam could be steered along left-right direction from -32.8° to 31°. This was demonstrated using finite element analysis simulations and experimentally proven on single-element prismatic transducers (7×6.9×10.6 mm3) operating at 133 kHz.
Ring-shaped transducers

Ring-shaped cylindrical biaxial driving transducers are built with two sets of electrodes: a pair on the top-bottom direction of the cylinder and a pair on the inner-outer surfaces. In ring geometry ferroelectric materials, we combine shear and extensional vibration modes as well to produce a controlled focusing that happens along the acoustic axis. This is achieved by controlling the phase between and the power ratio between the orthogonal fields.
The ultrasound beam can be steered from a depth of 5 mm to 20 mm. This steering was demonstrated using FEA simulations and experimentally validated for a 12 mm-radius ring transducer operating at 460 kHz.